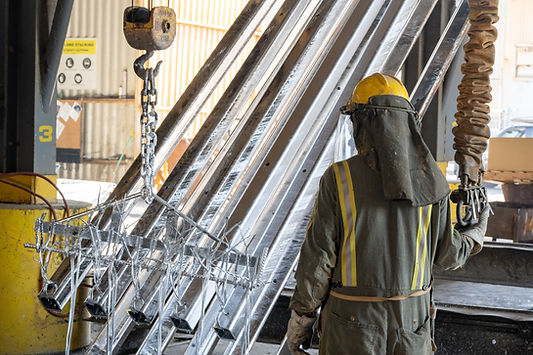
Design Considerations
In order to maximize the quality and effectiveness of the galvanization process, you’ll need to consider a number of factors before fabricating your product.
Consult with our team of experts as early as possible in the design process to take advantage of our years of experience, avoid common pitfalls and achieve a better overall product.
Video Guides
Learn about Galvanizing
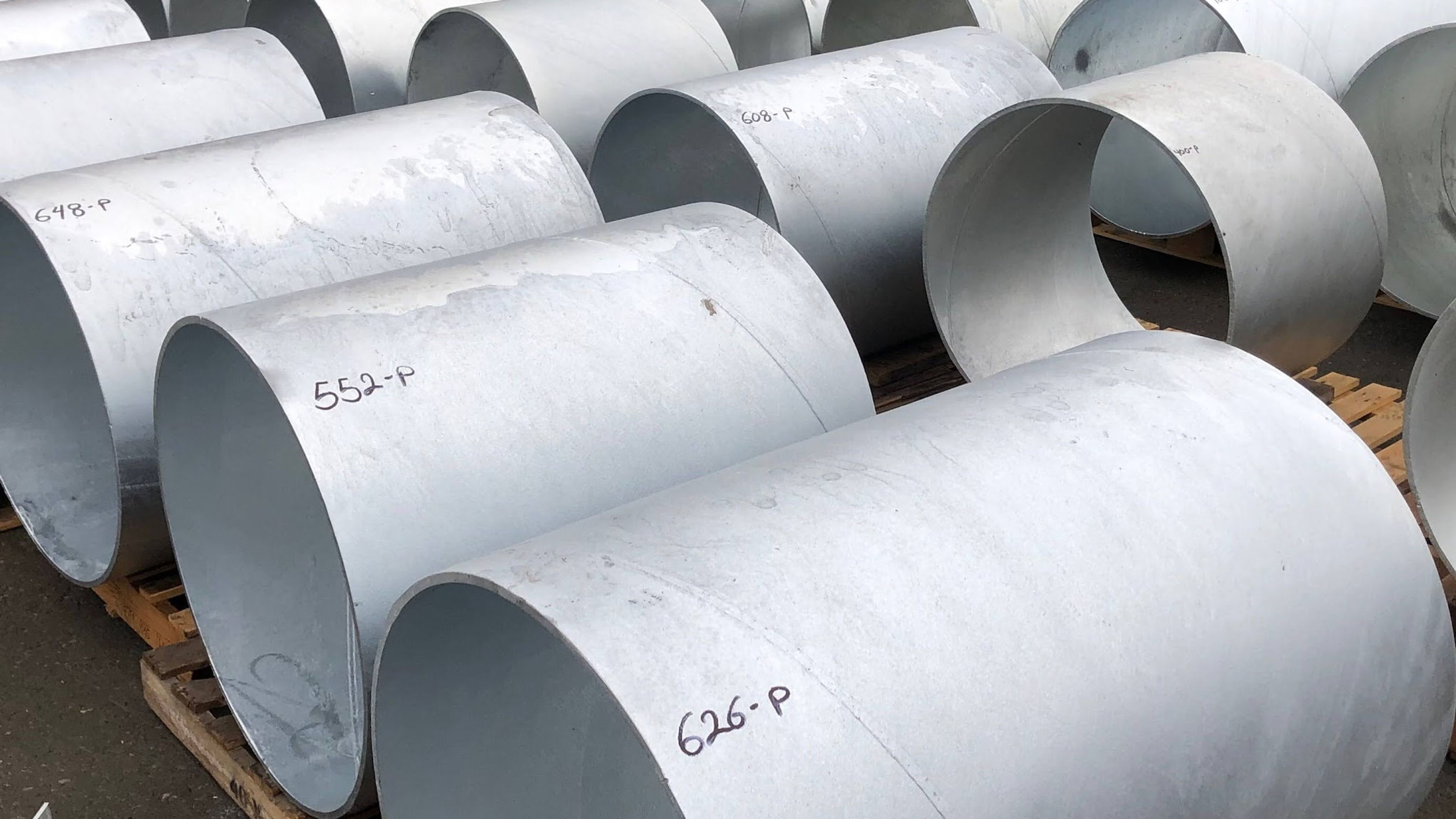

Pacific Galvanizing
Working with Base Plates
Handrail Venting
Marking your Project
Top Considerations
Venting and Drainage: To ensure that all interior and exterior surfaces of a product are protected from corrosion, the entire fabrication is lowered into cleaning solutions, flux solutions, and molten zinc. It will be important to incorporate strategically placed holes in the fabrication to optimize drainage and for air to escape to ensure the fabrication can be completely submerged.
Material Condition: Just like painting, galvanizing is all in the prep work. Stickers, glue, anti splatter, heavy rust, paint, or laquer are not cleaned off in the prep process, and can impact the final quality.
Size and Shape: Pacific Galvanizing has 2 kettles, 42’ x 4’ x 6’, and 14’ x 5’ x 6’. Often, certain design decisions need to be made to ensure that fabrications can properly fit in a galvanizing kettle. Consultation with our experts at the earliest stage of design will help you avoid common sizing errors.
Material Selection: Galvanization works better on some metals than others. A fabrication consisting of more than one material or with more than one type of steel may affect the quality and uniformity of the zinc coat and in some cases, fabrications could become susceptible to embrittlement and other complications.